Changing Visions into Fact: Aluminum Casting Illinois
Changing Visions into Fact: Aluminum Casting Illinois
Blog Article
Introducing the Art of Light Weight Aluminum Casting: A Comprehensive Overview for Beginners
In the world of metalworking, aluminum spreading stands as a craft that weds artistry with precision. Recognizing the nuances of this old method can be both appealing and gratifying, specifically for those venturing right into the world of casting for the first time. As novices start this journey, they are confronted with a maze of techniques, devices, and safety procedures that develop the foundation of grasping the art of light weight aluminum spreading. This comprehensive overview intends to demystify the procedure, providing a roadmap that navigates through the history, basics, alloys, preventative measures, and steps necessary for those seeking to produce their own aluminum spreadings.
Background of Aluminum Spreading

One of the key landmarks in the background of light weight aluminum spreading was the development of the very first light weight aluminum spreading machine in 1886 by Charles Martin Hall. Over the years, improvements in technology have better refined the light weight aluminum spreading process, making it much more accurate, economical, and ecologically friendly.
Essential Tools for Beginners
When getting started on the journey of aluminum spreading as a beginner, getting the important tools is critical for ensuring a successful and smooth casting process. A crucible, generally constructed from graphite or clay-graphite, is fundamental for thawing light weight aluminum. Crucible tongs are essential for managing the warm crucible securely. A furnace, either gas-powered or electric, is essential for thawing the aluminum to its fluid state. To get rid of impurities and solidified particles, a skimming tool is indispensable. A mixing pole helps in making sure and blending the molten light weight aluminum harmony. Flask and molding sand are essential for creating molds right into which the liquified light weight aluminum is put. A mold frame, including cope and drag, is needed for molding the sand. Airing vent rods help in producing channels for air and gas to escape from the mold throughout spreading. Ultimately, security equipment such as heat-resistant handwear covers, apron, and face shield are crucial for securing oneself during the spreading procedure. With these necessary devices in hand, newbies can start their aluminum casting trip with self-confidence.
Standard Actions in Light Weight Aluminum Spreading
To initiate the light weight aluminum casting procedure efficiently, newbies must first prepare the mold and mildew and ensure its appropriate positioning within the mold structure. As soon as the mold prepares, the next action entails melting the aluminum. This can be done using a heating system or a basic gas torch, relying on the range of the project. The molten light weight aluminum is after that carefully poured right into the mold, loading it to the border. It is vital to permit the light weight aluminum enough time to cool and strengthen inside the mold and mildew before attempting to remove the casting.
After the aluminum has cooled down and strengthened, the mold and mildew requires to be opened to disclose the newly developed spreading. Novices should wage care throughout this step to avoid damaging the mold and mildew or the spreading. The excess product, referred to as the sprue and any type of extra flaws, can be removed by sanding the spreading and cutting. Finally, the casting can be polished and finished according to the wanted requirements. Grasping these basic steps is essential for beginners looking to dig into the art of light weight aluminum spreading.
Common Sorts Of Aluminum Alloys
One of the crucial factors to consider in aluminum casting is comprehending the varied series of like this aluminum alloys commonly used at the same time. Aluminum alloys are classified based upon their chemical structure and residential properties, with each type offering unique features fit for different spreading applications. One common light weight aluminum alloy is A356, known for its exceptional castability and good mechanical properties, making it prominent in numerous industries such as auto and aerospace. Another extensively utilized alloy is 6061, valued for its high stamina and corrosion resistance, making it suitable for marine applications and architectural parts. Additionally, the 380 alloy is preferred for its superior fluidness and machinability, making it a top choice for complex castings calling for elaborate information. Recognizing the residential properties and benefits of these typical light weight aluminum alloys is important for beginner wheels to choose one of the most suitable alloy for their certain casting demands, making sure quality results in their spreading projects - aluminum casting illinois.
Safety Safety Measures in Spreading Aluminum
Thinking about the critical duty of light weight aluminum alloys in the casting procedure, prioritizing safety and security precautions is paramount to guarantee a protected and reliable spreading atmosphere. When working with molten light weight aluminum, it is important to wear proper personal safety tools (PPE) such as heat-resistant handwear covers, aprons, deal with shields, and safety and security goggles to stop injuries and burns. In addition, ensure correct ventilation in the spreading area to decrease exposure to harmful fumes and gases released throughout the melting procedure.
To prevent prospective fires, constantly have a fire extinguisher neighboring and establish a clear evacuation strategy in situation of emergencies. It is important to perform normal safety and security training sessions for all personnel included in the spreading operation to educate them on best practices and emergency situation treatments. Proper handling of equipment, consisting of crucibles, ladles, and molds, is essential to avoid crashes and keep a risk-free workplace.
Moreover, keeping a clean and well organized work space can assist lower the danger of slides, trips, and falls. By sticking to these safety and security precautions, beginners can develop a protected foundation for grasping the art of light weight aluminum spreading.
Conclusion
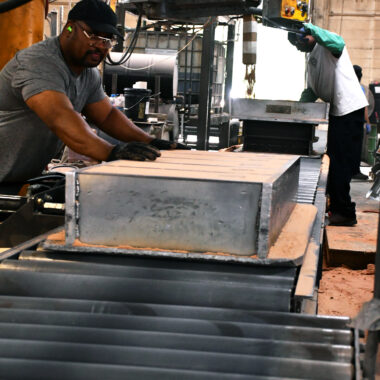
It was not until the 19th century that considerable advancements in aluminum spreading were made, especially with the growth of extra reliable methods for melting and forming aluminum alloys.
One of the crucial milestones in the background of light weight aluminum casting was their explanation the development of the initial aluminum casting device in 1886 by Charles Martin Hall.When getting started on the trip of aluminum spreading as a novice, acquiring the important tools is critical for guaranteeing a smooth and successful spreading procedure.One of the vital considerations in aluminum spreading is understanding the diverse range of aluminum alloys commonly made use of in the process. By recognizing the fundamental actions and crucial tools involved in light weight aluminum spreading, novices can successfully work with different kinds of aluminum alloys.
Report this page